Machine-onderdelen of gereedschappen slijtvaster maken kan door middel van thermische behandelingen. Maar dan moet het materiaal wel hardbaar zijn. Dus wat doe je met niet-hardbaar rvs, lager gelegeerde staalsoorten en non-ferro metalen? Hiervoor heef t Chromin uit Maastricht bijzondere oplossingen ontwikkeld gebaseerd op dif fusie van onder andere chroom, vanadium, aluminium en boor.
Mondiale speler
‘We zijn in 45 jaar tijd uitgegroeid tot een mondiale speler op dit specialistische terrein’, vertelt Remi Castermans, die als zoon van oprichter Leon Castermans de leiding heef t over het bedrijf dat rond de 25 medewerkers telt. ‘We kunnen onderdelen uit hoogwaardig staal veel duurzamer maken, terwijl onderdelen zonder in te boeten op levensduur en betrouwbaarheid ook vaak uit een goedkoper materiaal kunnen worden vervaardigd. Zoals waakvlambranders. Door zacht-inchromeren van relatief goedkoop, makkelijk te bewerken automatenstaal, krijgt zo’n brander een temperatuur- en oxidatiebestendigheid tot 850 °C waardoor de standtijd vrijwel oneindig wordt.’
Diffusietechniek
We behandelen werkstukken van een paar millimeter tot 9 meter’, vertelt Castermans. ‘Bij de dif fusietechniek hechten chroomdeeltjes zich bij een hoge temperatuur aan koolstofdeeltjes in het metaaloppervlak. Daarbij ontstaat chroomcarbide dat zeer hard is en een bijzonder dichte structuur heef t. Dat maakt het onderdeel zowel slijtvast als corrosie- en chemicaliënbestendig. Bij hardinchromeren zijn laagdiktes van 5-20 micron mogelijk en hardheden tot ± 2.000 Micro Vickers. Bij zacht-inchromeren praten we over laagdiktes van 35 tot 200 micron en hardheden tot 1.100 Micro Vickers.
Speciaal procedé
‘Vooral binnen de food- en farmasectoren wordt veel met roestvast staal gewerkt’, vervolgt Castermans. ‘Bij het ver- en bewerken van abrasieve grondstof fen (poeders/granulaten) en/of producten met een etsende werking zoals vetzuren, staan de onderdelen vaak bloot aan extreme slijtage en corrosie. Rvs bevat echter geen koolstof dus was het aanvankelijk niet mogelijk om deze van een hard oppervlak te voorzien door middel van inchromeren. Daar hebben we een oplossing voor ontwikkeld door eerst in een vacuümoven koolstof in het rvs-oppervlak te dif funderen. Daarna dompelen we het in chroompoeder van een speciale samenstelling. Bij verhitting in een oven tot zo’n 1.000 °C ontstaat dan het chroomcarbide waardoor het rvs slijtvast en corrosiebestendiger wordt. Het proces is milieuvriendelijk en volledig nauwkeurig te sturen qua laagdikte en hardheid en is momenteel internationaal gezien “big business”.’
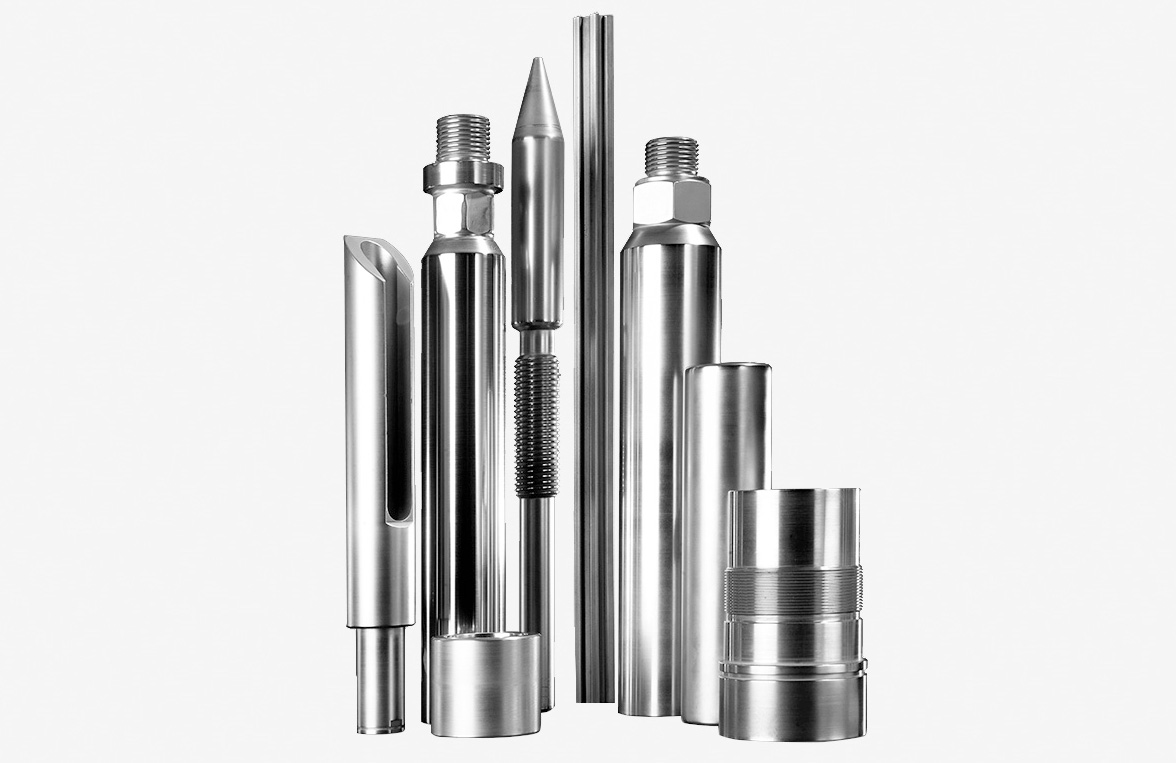
Harde laag op non-ferro
‘In de aluminiumen messingverwerkende industrie verhogen we de slijtvastheid door het dif funderen van vanadium’, zegt Castermans. ‘Vanaderen wordt bijvoorbeeld gebruikt voor omvormgereedschap, persdoorns, matrijzen en voor onderdelen in textielverwerkende machines. Met vanaderen zijn geharde lagen tot 3.000 Micro Vickers mogelijk! Een andere techniek is boreren, een thermisch-chemische oppervlaktebehandeling van ferrometalen, waarbij een hard en slijtvast oppervlak van ijzerboride ontstaat. Deze behandeling is erg geschikt voor onderdelen die worden blootgesteld aan abrasieve of adhesieve slijtage. Bij aluminiseren brengen we door middel van dif fusie aluminium in het oppervlak, waardoor zich aan het oppervlak aluminiumoxide vormt. De temperatuurbestendigheid neemt daardoor toe tot wel 1.500 °C. Veel voorkomende toepassingen zijn warmtewisselaars en ferrules in de chemische en petrochemische industrie. Ook voor componenten in elektriciteitscentrales wordt aluminiseren veel gebruikt. Naast de genoemde technieken kunnen we ook thermisch harden en plasmaspuiten, waarbij we extreem harde lagen op basis van keramische of carbide materialen kunnen aanbrengen.’
Accent op duurzaamheid
In 2014 zijn we voor de automotive industrie gaan werken waardoor de seriegroottes enorm toenamen’, vertelt Castermans. ‘We begonnen met 1.000 onderdelen per maand, nu zijn dat er 120.000, waaronder turbo-componenten die slijtvast en hittebestendig moeten zijn. We hebben veel aandacht voor de duurzaamheid en milieuvriendelijkheid van onze processen. De poeders worden na opwaardering bijvoorbeeld hergebruikt. Ook liggen onze daken vol met zonnepanelen en daarnaast hebben we onlangs geïnvesteerd in een nieuwe geavanceerde doorloopoven waarmee we continu kunnen werken (temperatuur blijf t constant). Daarmee gaan we ten opzichte van de kleinere batch-ovens veel elektriciteit besparen. Door het proces bovendien in een stikstofatmosfeer te laten plaatsvinden hoeven we niet meer met glasseals te werken om het proces hermetisch af te sluiten, wat eveneens voordelen oplevert. Kortom, we blijven innoveren want er zijn altijd mogelijkheden om iets beter, sneller, ef fi ciënter en/of duurzamer te doen.’